В промышленности применяются следующие виды сварки:
- электрическая сварка
- газовая сварка
- кузнечная сварка
- термитная сварка
- сварка трением сварка
Электрическая сварка делится на:
-
электродуговую сварку прямого и косвенного действия
-
контактную сварку, к которой относятся пиковая, точечная и шовная сварка
Электродуговая сварка впервые появилась в XIX столетии. Ее осуществили русские инженеры Н. Н. Бенардос и Н. Г. Славянов. По ГОСТ 9467-75 предусмотрено большое количество марок электродов, которые имеют вполне определенные области применения в зависимости от марок свариваемых сталей. Диаметр электродов выбирается в соответствии с толщиной свариваемых листов и размеров шва. Чем толще лист, тем больше диаметр электрода. Процесс сварки сопровождается выделением от дуги ослепительного света и разбрызгиванием расплавленного металла. Поэтому сварочные работы выполняются рабочими в брезентовой прозодежде, в рукавицах, со щитками, имеющими темные стекла, снижающими яркость дуги. Из разновидностей дуговой сварки за последнее время широкое распространение получила сварка под слоем флюса и сварка в среде углекислого газа. Флюс и углекислый газ являются предохранительной средой от загрязнений, обеспечивающей высокие механические свойства направляемого металла. При этом в состав флюса вводят шлакообразующие составляющие, раскислители и легирующие составляющие. Оба метода сварки сопровождаются применением автоматизации.
Для приварки к листу шпилек (стержней) применяются специальные сварочные устройства – пистолеты. Контроль сварочных швов без разрушения конструкций в особо ответственных случаях осуществляется с помощью ультразвука, рентгеноскопии, гамма-лучей. ПО техническим возможностям оба метода обеспечивают надежность проверки качества сварки и позволяют выявлять местные пустоты (незаполнение), пленистость, пористость и другие дефекты на всей глубине сварочного шва. Для контроля углеродистых сталей с толщиной стенки до 12 мм применяется магнитографический дефектоскоп. Для тех же сталей при толщине стенки свыше 15 мм используется ультразвуковой дефектоскоп. Контроль аустенитных сталей с толщиной стенки от 20 до 50 мм целесообразнее производить гамма-просвечиванием или использовать ультразвуковую дефектоскопию.
Дефекты, выявленные в ответственных сооружениях (трубопроводы высокого давления), подлежат устранению, после чего контроль выполняется повторно.
Основные разновидности типовых сварных соединений:
-
соединение стыковое
-
в нахлестку
-
тавровое
-
угловое
Электродуговая сварка требует подготовительных работ в части разделки скосов и снятия фасок. Эту работу обязан выполнять слесарь-монтажник. Разделка скосов и снятие фасок перед сваркой делаются для того, чтобы получить шов, имеющий не менее 80% прочности целой детали. Для тонких листов (до 2 мм) под сварку делается отбортовка и шов накладывается сверху. При сварке листов толщиной 2-5 мм допускается бесскосное соединение. В этом случае расплавленный металл электрода должен заполнить разрыв в l-З мм между листами. Свариваемые листы толщиной 5-15 мм требуют подготовки кромок в виде V-образных скосов, причем с утолщением листа угол развала увеличивается до 90°. Образовавшееся углубление заполняется металлом шва, и этим гарантируется необходимая прочность. Для сварки толстых листов, более 15 мм, применяют X-образные скосы указанных размеров. В условиях монтажных работ обработка кромок и подготовка скосов у листов делается ручным и пневматическим зубилами или с помощью газовой резки. Обработка на металлорежущих станках применяется в тех случаях, когда свариваемые изделия изготовляются в специализированных цехах. При сварке неплоских деталей, кроме подготовки скосов, приходится отдельные детали крепить до прихватки струбцинами и другими средствами. После прихватки и проверки правильности установки свариваемых деталей снимают крепежные средства и приступают к окончательной сварке.
Различают также холодную и горячую сварку.
Горячая электродуговая сварка делается с предварительным подогревом свариваемых деталей до t = 600-700° (в особо ответственных случаях, главным образом у чугунных деталей). Во всех остальных случаях при сварке железных конструкций применяется холодная дуговая сварка. После сварки для снятия остаточных напряжений ответственные металлоконструкции следует подвергать отжигу. Этот метод сварки применяется в ремонтной практике при реставрации изношенных деталей.
Кроме сварки, электродуговой метод применяется при резке металлов. Резка производится угольным (графитовым) электродом с толстой обмазкой. Разрез получается неровный, а процесс обработки – малоэкономичный. Электродуговая резка иногда применяется при разделке металлического лома и при отрезке литников и прибылей у стальных, чугунных и других отливок.
Электроконтактная сварка производится на специальных сварочных машинах. Для нагревания свариваемых изделий используют теплоту, выделяющуюся в точках наибольшего сопротивления электрической цепи. Такими точками являются места соприкосновения деталей, подлежащих сварке.
При стыковой сварке, являющейся разновидностью электроконтактной сварки, ток напряжением 1-З В подводится от специального понижающего трансформатора. При этом свариваемые детали сближаются до соприкосновения. В месте стыка возникает температура плавления металлов, и тогда, выключив ток, детали сдавливают друг с другом дополнительно. Стыковая сварка применяется при сварке инструмента, в котором быстрорежущая сталь сваривается с углеродистой. Недостатки метода – нарушение структуры и большой расход электроэнергии
При точечной электрической сварке соединяемые детали из тонкого листа сдавливаются между двумя электродами, И которым подведен ток 2-10 В. Вследствие большого сопротивления место контакта нагревается до температуры сварки и под действием силы сжатия детали свариваются в данной точке. Оба электрода (подвижный и неподвижный) изготовляются из медного сплава с большим поперечным сечением. Благодаря высокой электро- и теплопроводности они не привариваются к деталям. Точечные аппараты имеют высокую производительность: дают до 2000 точек сварки в час.
Шовная сварка применяется для соединения тонких листов (до 3 мм) из низкоуглеродистой стали, нержавеющей стали, латуни и алюминиевых сплавов. Шовная сварка широко применена при изготовлении тонкостенных электросварных труб на трубопрокатных заводах. Сварочная машина подобна аппаратам точечной сварки с той лишь разницей, что ее электроды представляют собой вращающиеся ролики, между которыми пропускаются свариваемые листы. При сварке образуется непрерывный шов, обеспечивающий высокую прочность и герметичность соединения.
Из разновидностей газовой сварки наибольшее применение нашла кислородно-ацетиленовая сварка. При газовой ацетиленово-кислородной сварке нагревание кромок спариваемых деталей, а в равной степени и плавление присадочного материала, заполняющего впадину и образующего шов сварки, производится в пламени ацетилена, сгорающего в кислороде. Для сжигания указанной горючей смеси используется специальная сварочная горелка, куда поступает из баллонов кислород под давлением 2,5-3,5 атм и ацетилен при давлении 0,l-0,5 атм. Наибольшая температура в зоне сварки достигает 3000°.
Газовая сварка применяется при ответственных сварочных работах из листового материала, малоуглеродистой конструкционной стали, а также при сварке различных цветных металлов и сплавов и при запарке чугунных деталей. Присадочный материал в виде нарезанных прутков по своему химическому составу должен быть близким к материалу свариваемых деталей. Подготовка кромок и скосов под сварку осуществляется так же, как и для электродуговой сварки. Для чугунных изделий после сварки необходимы равномерное охлаждение и последующий отжиг.
Газовая резка основана на сгорании металла в струе кислорода. Для резки металла применяются специальные горелки-резаки. Через центральный канал резака подается кислород под большим давлением, а по кольцевому каналу поступает ацетилено-кислородная смесь, которая нагревает металл свариваемых деталей до температуры воспламенения.
При этом в струе кислорода происходит быстрое сгорание металла и продукты окисления в виде шлака выбрасываются струей наружу. Основное назначение газовой резки – вырезка заготовок из листов конструкционной, углеродистой и других марок сталей.
Перед началом вырезки очищают лист и размечают на поверхности требуемые заготовки. Зачистку поверхности листа от окалины производят механизированно-ручным способом металлическими щетками и предварительным нагревом листа пламенем горелки. Отрегулировав газорежущее пламя горелки, приступают к вырезке заготовок. Резку всегда начинают от внешней кромки и ведут резак, перекатывающийся на роликах, по намеченным рискам. Качество газовой резки и ее производительность зависят от подогревающего пламени, а также от равномерности и скорости передвижения резака и его расстояния от поверхности разрезаемого металла. Подогревающее пламя должно обеспечивать быстрый нагрев детали в начале резки и максимальную скорость резки. Оно должно быть узким и достаточно длинным. Во время резки следует стремиться делать наименьшую ширину реза, избегать оплавления и науглероживания кромок вырезаемых деталей. Ручная газовая резка в настоящее время применяется сравнительно мало. Она заменена машинной резкой.
Применяется также высокопроизводительная плазменная резка листов. Это резко повышает производительность и улучшают качество работ. Глубина прорезания кислородной струей может достигать одного метра и более, поэтому этот вид резки имеет неограниченное применение при разделке различных болванок, броневых листов и даже применяется под водой при разрезании затонувших корпусов судов. Чугун, алюминий, медь и ее сплавы газовой резке не поддаются, так как температура воспламенения у этих металлов выше температуры плавления.
Кузнечная сварка состоит в том, что разогретые концы двух стальных свариваемых деталей накладываются друг на друга и место соединения проковывается вручную или под молотом. В процессе проковывания при t~ l400-l460°C происходит диффузия частиц металла и обеспечивается достаточно прочное соединение.
Термитная сварка основана на способности термита (порошковая смесь металлического алюминия с железной окалиной) при воспламенении давать высокую температуру. При этой температуре (2300-3000°) восстанавливается из окиси железо, которое в жидком состоянии заполняет ванну и образует сварочный шов; высвободившийся из окиси железа кислород частично сгорает, а частично вступает в соединение с алюминием, образуя окись алюминия в виде падежной защитной пленки на поверхности сварочного шва. Термитная сварка, так же как и кузнечная, применяется ограниченно, например при сварке рельсов, что, видимо, объясняется большой трудоемкостью и малой производительностью этих методов.
Для сварки аналогичных деталей и инструментов встык в настоящее время применяется метод сварки – трением. Сварка выполняется на специальном оборудовании. Две заготовки из разных или одинаковых металлов зажимаются в приспособления, торцы их сближаются друг с другом. При этом одной из деталей сообщается вращение. В результате трения при вращении заготовки возникает высокая температура и оплавляются торцы. Вращение останавливают и дают дополнительное сдавливание, в результате чего получается надежное, прочное соединение. Сварка трением пока еще широкого промышленного распространения не получила, однако этот вид сварки имеет ряд преимуществ в сравнении с электроконтактным методом (повышенная прочность, отсутствие газовых выделений и пр.). Метод вполне пригоден для сварки деталей небольших размеров, изготовленных из стали, меди, алюминия, латуни и других материалов.
Еще используется метод, так называемой холодной сварки. Он основан на пластической деформации металла. Применим для сварки цветных металлов одноименных и разноименных марок. Процессу сварки предшествует хорошая зачистка соединяемых поверхностей. После зачистки оба образца сближаются торцами и их сдавливают друг с другом на специальном пневматическом прессе. После сдавливания получается надежное, прочное соединение, основанное на пластической деформации и диффузии металлов. Метод сварки назван холодным потому, что образцы при сдавливании остаются совершенно холодными
Внимание покупателей подшипников Уважаемые
покупатели, отправляйте ваши вопросы и заявки по
приобретению подшипников и комплектующих на почту или
звоните сейчас:
+7(499)403
39 91
Доставка подшипников по РФ и зарубежью.
Каталог подшипников на сайте themechanic.ru
|
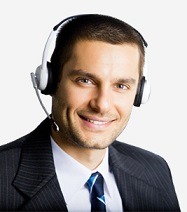
Внимание покупателей подшипников
Уважаемые покупатели, отправляйте ваши вопросы и заявки по приобретению подшипников и комплектующих на почту или звоните сейчас:
+74993506619
zakaz@themechanic.ru
Доставка подшипников по РФ и зарубежью.
Каталог подшипников на сайте
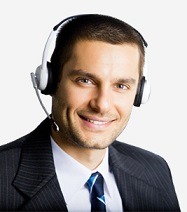
Внимание покупателей подшипников
Уважаемые покупатели, отправляйте ваши вопросы и заявки по приобретению подшипников и комплектующих на почту или звоните сейчас:
+74993506619
zakaz@themechanic.ru
Доставка подшипников по РФ и зарубежью.
Каталог подшипников на сайте